抢抓施工黄金季,海太长江隧道“江海号”盾构机掘进突破百环大关
5月2日上午,位于长江入海口的世界上最长公路水下盾构隧道——海太长江隧道,正如火如荼建设,正在施工作业的“江海号”盾构机顺利掘进至200米,突破百环大关,工程建设取得阶段性进展。
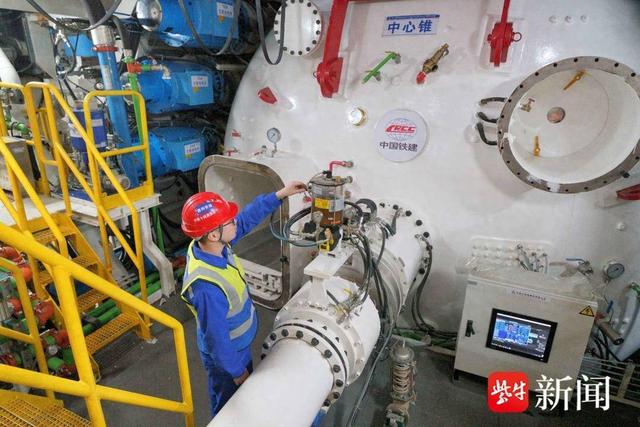
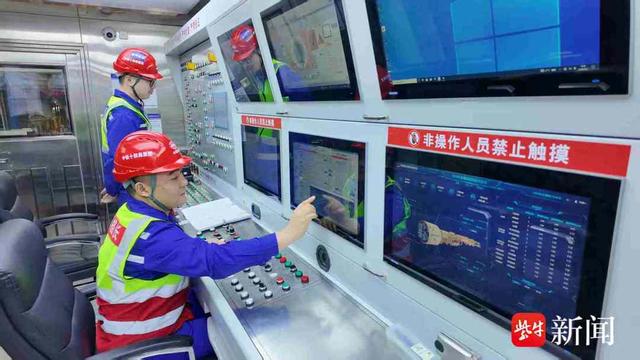
海太长江隧道工程位于江苏省长江入海口区域,北起南通海门区,南至苏州太仓市,线路全长39.07公里,其中过江隧道全长11.185公里,采用双向六车道高速公路设计标准,设计速度为100公里每小时,为全线重点控制工程。中铁十四局负责的隧道盾构段长9315米。
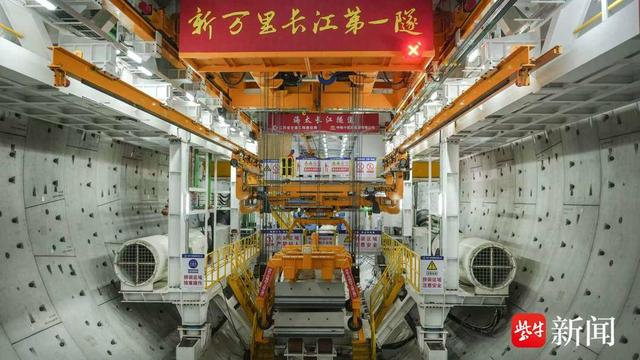
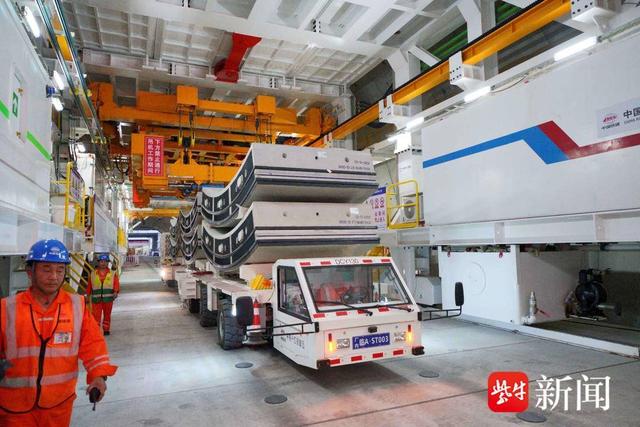
中铁十四局海太长江隧道项目盾构经理孟德锋介绍,盾构段需要长距离穿越长江底淤泥质粉质黏土夹粉土、粉细砂复合地层等复杂地质带,最大埋深约75米,最高水压达7.5巴,具有超长距离、超大直径、超高水压、超大埋深、复杂工况等特点。项目团队结合多年来在水下和大直径盾构隧道施工经验,为工程“量身定制”一台国产16米级超大直径泥水平衡盾构机“江海号”进行施工。
走进最大开挖直径达16.64米的“江海号”盾构机内部,宽敞明亮,掘进有序。“这台崭新的设备,在刀盘刀具、主驱动、推进等九大系统进行创新攻关,配备了常压刀盘、主驱动在线监测系统、HSP超前地质探测预报、第四代同步双液注浆、DDCI自动拼装装置等先进技术,总装达到世界先进水平。”中铁十四局海太长江隧道项目盾构机长刘昕介绍,在盾构机工厂制造和现场组装调试阶段,项目提前组织掘进班组进行针对性系统性培训,从排查线路开始,了解每个部件的功能,掌握其操作技能,尤其针对主机性能操作,会在以往经验的基础上再深入学习,包括如何来控制盾构姿态、掘进速度、分析故障、调控参数等,始发掘进后真正进入人机磨合期。

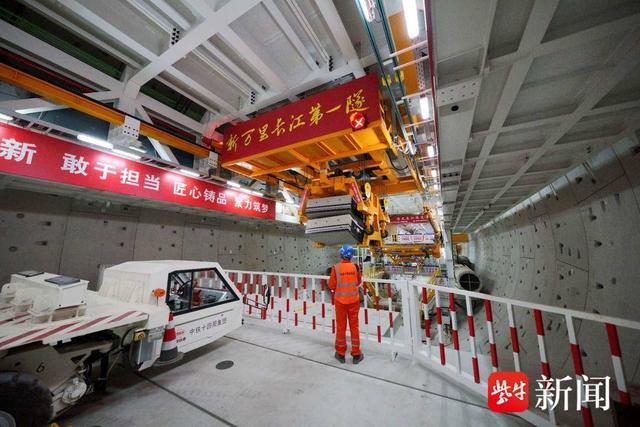
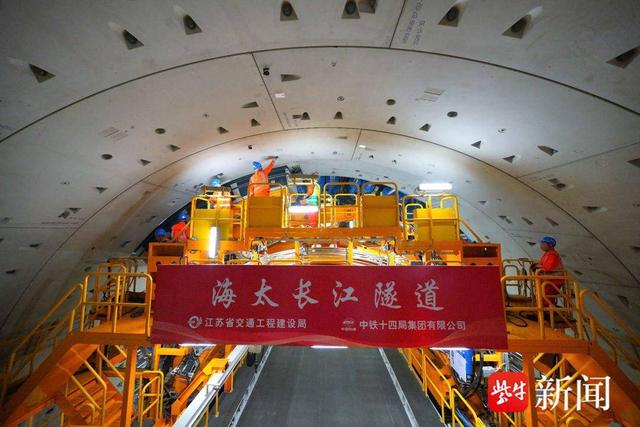
如何克服浅覆土始发、保证箱涵高效运输和拼装、保证DDCI新型连接构件拼装效率是掘进初始阶段需要解决的难点问题。尤其是隧道内部采用整体式全预制箱涵,单块最大总重约45吨,长约13.5米,宽1.5米,高约5.05米,为目前国内隧道内部最大预制构件,超宽超大件给运输和拼装带来极大难度。
自4月9日始发掘进以来,中铁十四局项目团队加强方案优化,采取专业化措施一一分析解决,通过优化双液浆配比,并控制好同步注浆压力和注浆量,确保成型隧道质量。项目提前对管片拼装团队进行DDCI构件拼装技术交底,通过同步优化工序安排、提高自动化程度等方式确保拼装效率。项目还对箱涵运输车辆进行针对性设计,配备车身大幅度升降功能,提升旋转功能及良好的制动性能和爬坡能力。
“项目顺利完成‘百环试验段’,在总结经验的基础上,加强人机磨合,掘进速度由原来的日掘进4米提升至日掘进14米左右。目前,成型隧道外观良好,质量可控,各项指标均满足设计和规范要求。”中铁十四局海太长江隧道项目高级工程师宋欢表示,“五一”期间,有300多名工人持续奋战在隧道施工一线,24小时轮班值守,全力确保施工进度安全有序推进。
刘昕说,经过近一个月的时间,隧道顺利突破百环大关,成功渡过人机磨合期。100环的成功掘进经验,让他们团队从小心翼翼转变为心中有数,虽然每天重复地忙碌作业,但他们依然很开心,因为“江海号”已顺利掘进,朝着对岸平稳前行。
未来隧道建成后,车辆过江仅需10分钟,从南通海门这里出发,半个多小时就能到达上海市中心。工程的建设,对于贯彻落实长三角区域一体化发展战略,推动长江两岸城市群的跨江融合发展等,都具有十分重要的意义。
通讯员 董凯
发表评论:
◎欢迎参与讨论,请在这里发表您的看法、交流您的观点。